Service
Question 1. Analysis and solutions for fault causes of excavator traveling device
1. Cracked track chain link
1.1 Reason Analysis
After the excavator has been working for a period of time, in addition to the wear of the track shoes, sometimes the track link rail joints will also crack, as shown in Figure 1. When designing crawler track link joints, static analysis is performed on them. The analysis results show that the maximum stress values of the crawler track link rail links themselves are less than the material yield limit and can meet the strength requirements. Therefore, the fault can be determined to be that during the actual operation of the excavator, the track link rail joints were repeatedly subjected to alternating loads, causing fatigue damage to the material and leading to cracking.
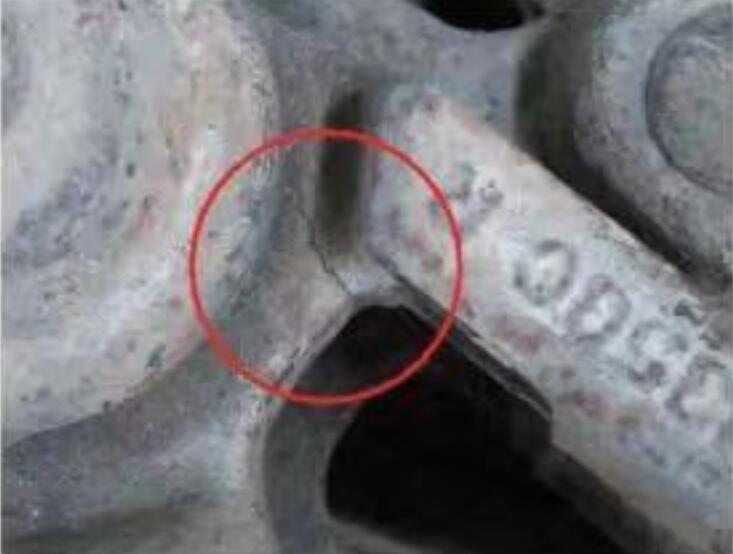
1.2 Solution
When designing track link links, the fatigue damage limit of the material should be fully considered. To this end, the fatigue analysis module in RecurDyn (dynamics simulation software) can be used to establish a virtual model of the excavator prototype and perform dynamic simulations. The analyzed crawler link rail segments can be flexibly subjected to rigid-flexible coupling simulation, set material properties and use The rigid-flexible coupling results are used to perform fatigue analysis on the track link rail segments. Through fatigue life analysis, the fatigue damage limit of the excavator track link joints under simulated working conditions can be predicted, and the structure of the track link links can be improved based on this.
1.1 Reason Analysis
After the excavator has been working for a period of time, in addition to the wear of the track shoes, sometimes the track link rail joints will also crack, as shown in Figure 1. When designing crawler track link joints, static analysis is performed on them. The analysis results show that the maximum stress values of the crawler track link rail links themselves are less than the material yield limit and can meet the strength requirements. Therefore, the fault can be determined to be that during the actual operation of the excavator, the track link rail joints were repeatedly subjected to alternating loads, causing fatigue damage to the material and leading to cracking.
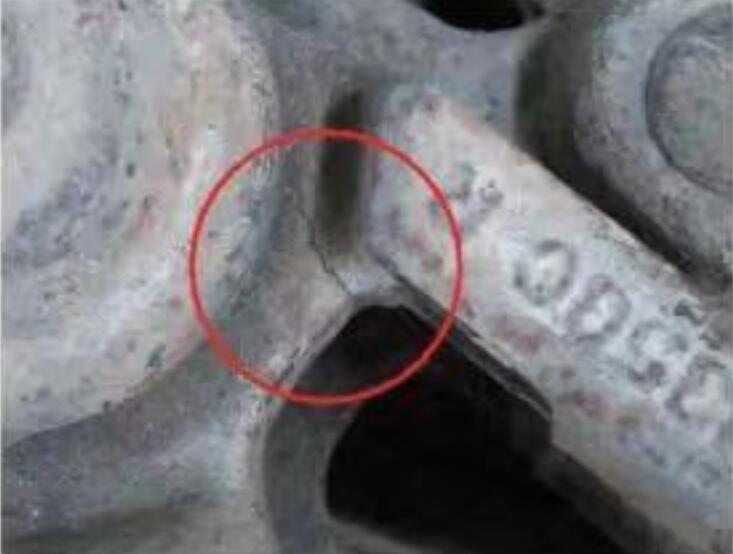
1.2 Solution
When designing track link links, the fatigue damage limit of the material should be fully considered. To this end, the fatigue analysis module in RecurDyn (dynamics simulation software) can be used to establish a virtual model of the excavator prototype and perform dynamic simulations. The analyzed crawler link rail segments can be flexibly subjected to rigid-flexible coupling simulation, set material properties and use The rigid-flexible coupling results are used to perform fatigue analysis on the track link rail segments. Through fatigue life analysis, the fatigue damage limit of the excavator track link joints under simulated working conditions can be predicted, and the structure of the track link links can be improved based on this.
Service
Contact Us
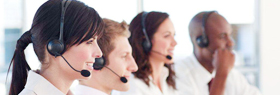
Name: Catherine
Tel: +86-15711791591
E-mail: [email protected]
E-mail: [email protected]
E-mail: [email protected]
E-mail: [email protected]
Skype: wkzparts01
Skype: wkzparts02
WeChat: wkzparts01
Whatsapp: 15711791591
Add: C107 HuiShun Business Buildinig No.99 Donghuan Road Zhucun Guangzhou,China